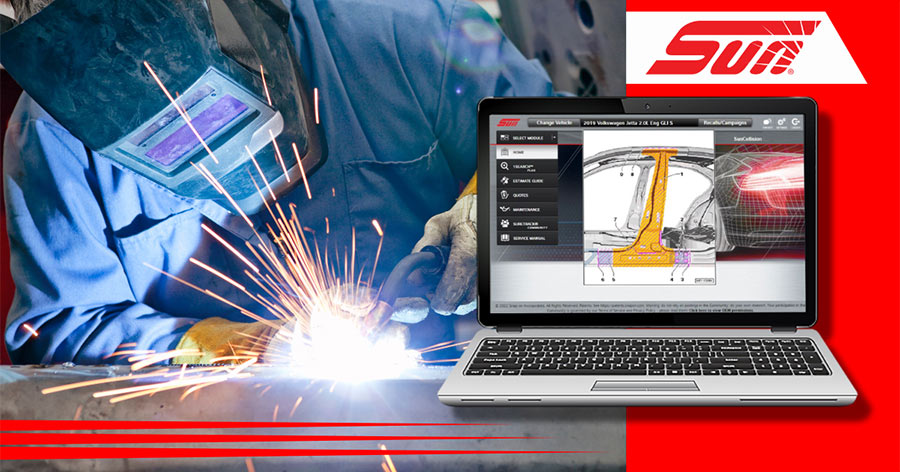
Best Practices for Collision Repair in Autobody Shops
By
|Does your body shop follow the industry’s best practices? Not merely conventional auto body shop best practices, but also the latest procedures to keep pace with the ever-changing auto industry? There is no substitute for experience—every seasoned tech knows that. But some tools and processes can help take even the most experienced technician’s skills to another level.
Imagine combining the experience of your body shop technicians with the most up-to-date practices and technology. Successful collision shops invest in innovative tools for scheduling, quality control, training, and diagnostics to stay current. They also invest in cutting-edge technology for modern customer communications and advanced diagnostics.
Implementing collision repair best practices has always been a winning move, regardless of the era. The difference today is those practices are more technologically advanced and cover a much broader scope. But when body shops invest in the latest digital tools like SUN® Collision Repair Information, they can keep up and move ahead.
#1 Follow OEM Collision Repair Standards
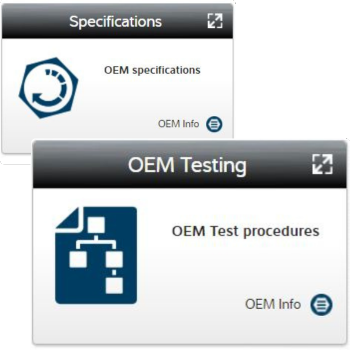
A standard operating procedure in body shops is to follow OEM specifications for safe and accurate repairs. More than ever, up-to-date OEM repair information is critical to your body shop’s success. OEMs know their products inside and out and provide the guidance and specifications technicians need to work on modern vehicles. When your collision facility makes OEM standards the golden rule, almost every aspect of your business benefits.
OEM information is the most consistent and cost-effective resource for nearly every repair. From diagnostics to the final coat, having on-demand access to OEM repair specifications can take your business to another level. When you embrace technology like collision repair software, the results are more skilled technicians, higher-quality repairs and streamlined operations. If you want increased profit to be a standard procedure for your body shop, invest in the latest auto body shop best practices with the latest repair technology.
#2 Master the Art of Scheduling
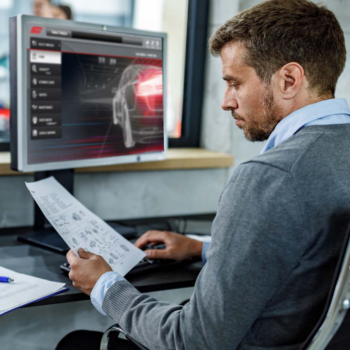
How efficient is your body shop’s workflow? Does the day’s work stop and start repeatedly, or is it a continuous stream of productivity? For most facilities, the answer lies somewhere in between. Implementing tools like repair software to easily access the latest OEM repair specifications will increase productivity and ensure better repairs. Regardless of how much technology and updated information you have, you will never realize the full benefits unless you master scheduling.
Consider that every vehicle at your shop equates to revenue and profit. How can you maximize your auto body shop’s processes and keep those repairs flowing? Detailed scheduling. The mere act of mapping out your shop’s scheduling will expose areas that impact cycle times. A basic schedule that includes the arrival date, repair start date, completion date, and delivery date is the foundation for an organized workflow. The formula is simple—the more you know about the status of each vehicle in your shop, the better you can plan the repair process and meet unexpected challenges.
We all know inaccurate and incomplete estimates can skew projected labor hours, and that’s all it takes to derail the repair. You can alleviate many of the traditional delays and productivity-killers with automated work packages—but even the most well-planned strategy will have hiccups. Changing gears on the fly and rescheduling is much more manageable when you follow an up-to-date schedule daily.
#3 Make Quality Control a Part of Every Repair Process Step
Following OEM repair standards and an efficient and flexible scheduling system will help create greater efficiency. But how do you know if the completed repair meets OEM standards? Remember—the auto industry changes fast, and learning how to complete a repair doesn’t always mean the repair is up to standards. The only way to ensure every repair in your shop is safe, accurate, and profitable is to inspect what you expect.
If you don’t want to be surprised by a comeback or a bad review, a quality check at each stage of the repair process is necessary. Following up on each repair step may seem like a lot, but the payoff of better repairs, happier customers, faster turnarounds, and more profit, definitely proves worthwhile. Optimally, you or a manager will conduct the QA inspections to ensure OEM compliance. If your technicians are experienced enough, they can handle the QA for the step preceding their step.
Quality control is more than a collision repair best practice for ensuring everything is on schedule and up to par. When a body shop owner or manager isn’t part of the inspection process, a QA checklist is a resource for reviewing performance. You don’t have to have your hands on every job when you have documentation of the repair process. A weekly review of QA checklists will help you identify performance and efficiency issues and opportunities for training.
#4 Invest in Training and OEM Certification

A streamlined and modern body shop will attract the best candidates in an industry desperate for new talent. Comprehensive and ongoing training will help retain them and add value across your services. Not only can your technicians perform better repairs and talk the talk—they can also assist with quality control, scheduling, and other aspects of running the business.
A collision technician up-to-date on the latest OEM processes is more confident and skilled. These knowledgeable professionals will be better equipped to work with customers and insurance companies. What training gives your business the best return? No training will deliver more value than OEM Certification.
An OEM Certified auto body shop is highly regarded by customers and insurance companies, leading to higher volume. OEM Certification ensures safe and accurate repairs, instills customer confidence, and gives technicians the advanced tools they need to become a pro. Invest in OEM Certifications and reap the benefits: advanced technicians, safe and accurate repairs, and a healthier bottom line.
#5 Streamline Collision Repairs with Advanced Diagnostics
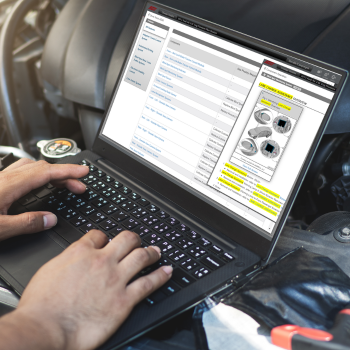
Put the first four auto body shop best practices to work in your body shop, and you’re already ahead of the competition. Invest in advanced diagnostics, and you can pull away! What would it mean for your cycle times if every diagnosis were fast, accurate, and easy to understand? You know how critical the diagnostic step is for the repairs that follow. Get it wrong, and you lose time, money, and maybe even customers. Get it right, and you can fast-track the repair process and deliver the high-quality service OEMs demand, and customers love.
To get it right every time, only the latest and most comprehensive diagnostic tools for everything from ADAS to frame rails will do. SUN Collision provides the most current OEM repair information and a full database of real-world repair information. Imagine having detailed OEM diagnostic data and insights from technicians who have completed the same repair for every job. Getting off on the right foot starts with the most complete diagnosis, and no other step of the repair process will have more impact.
#6 Make Customer Relations a Priority
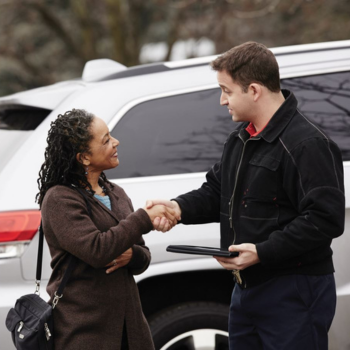
Your customers are more informed than they used to be about what a body shop should and shouldn’t do. This knowledge makes them more selective when choosing a body shop but no less thrilled at good old-fashioned customer service. The best body shops in the industry consider customer relations to be as crucial as quality repairs. These top collision centers understand the value of exceptional service to customers and insurance companies.
The benefits of high-level customer service are well known—and every body shop owner likely knows what great customer service means. To most, it means the customer is the priority. The above collision repair best practices contribute to excellent customer relations for evident reasons. Fast and accurate repairs create happier customers, but you must be sure you’ve raised the bar high enough. Whether you rely upon online reviews, feedback from surveys, or ratings from a postcard (maybe all three?), you can discover vital information.
#7 Implement Sustainable Practices
We get it. The collision repair process creates byproducts that aren’t exactly bio-friendly. Much of the materials used in body shops can’t be recycled or easily disposed of. But you can take steps to make your repair processes more sustainable and less hazardous. Non-toxic degreasers, sealed floors, drip pans for transfer, and preventive measures to keep runoff out of public drain systems are a good start.
Yes, going green can cost you some green. But the benefits are many. Adding sustainability to your body shop’s best practices is good press and good for profits. Many of your prospective customers want to do business with companies that care about the environmental impact of their services. Depending on the level of sustainability your shop achieves, you could also enjoy tax credits, incentives, and lower insurance rates.
Prepare Your Auto Body Shop for the Future
Best practices such as following OEM repair procedures, investing in training, and going green can help grow your body shop. When the repair process is smooth, and customers are satisfied, everything else just seems to fall in place.
Let SUN Collision help you pull all the pieces together with the most advanced collision repair software available. Get your free, no-obligation demo or talk with a collision repair professional at 877-840-1973 today.
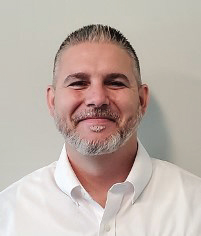
Chris Bonneau is the Business Manager for the SUN Collision product line. He has been in the automotive repair and collision industry since 2006. Chris has served in several roles at Snap-on, including Regional Sales Manager for the Southeast United States and Supervisor of the Mitchell 1 SocialCRM Marketing Services. Chris is also an alumni of San Diego State University.