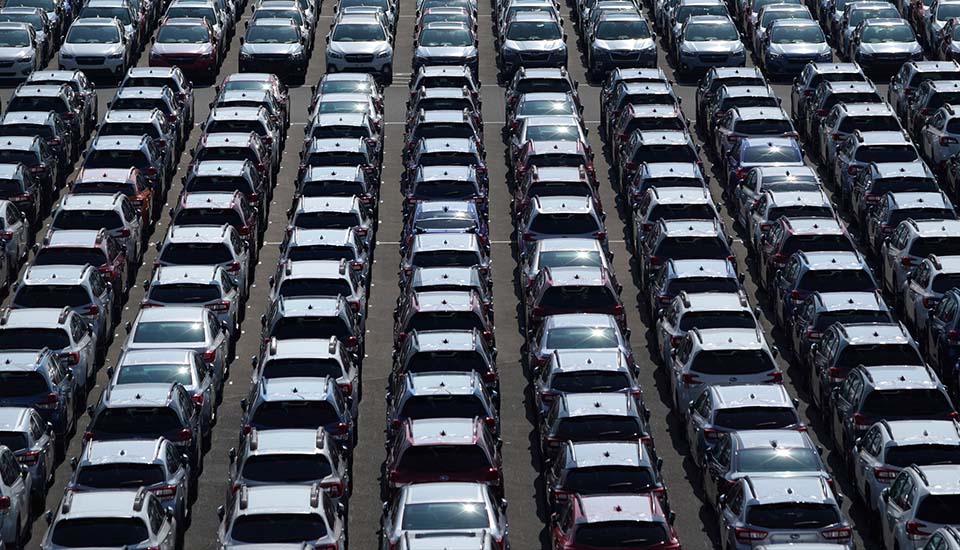
Get the Scoop on Vehicle Recalls and Technical Service Bulletins
By
|Vehicle recalls and Technical Service Bulletins (TSBs) seem to occur all the time in the auto industry, involving either critical safety repairs or manufacturing defects. Both address the performance and safety of a vehicle, but it’s important to know the difference between the two and how to deal with these issues.
Recalls occur when manufacturers identify a serious defect that may compromise the safety of the vehicle and its passengers. Auto recalls are sent to vehicle owners advising them to take their car to an authorized dealer or service center.
TSBs are created when the manufacturer, or more often, a repair technician, discovers problems after a vehicle goes into service. These service bulletins aren’t typically safety-related, but if left uncorrected, could create safety and performance issues. The purpose of service bulletins is to provide repair or replacement procedures to repair shops so they can correct the issue.
What Are Auto Recalls?
Vehicle recalls are typically issued when a vehicle or equipment on the vehicle has a safety defect or fails to meet the Federal Motor Vehicle Safety Standard. Standards are set for all safety-related components including headlights, brakes and wheels to ensure a vehicle meets minimum performance standards. Safety features that protect vehicle occupants such as ADAS, seat belts and airbags are also strictly regulated.
Typical recalls are usually classified as either safety-related or non-safety-related issues. Safety-related issues will prompt a recall when those issues pose a risk to vehicle occupants and will often cover a group of vehicles or vehicle components.
Common safety-related vehicle recalls include the following:
● Steering components that fail or malfunction
● Windshield wipers that are faulty
● Gas pedals or brake pedals that stick or break
● Seats that don’t stay in place
● Wiring systems that short or otherwise malfunction
● Wheels that don’t meet safety standards
● Components of ADAS that don’t work properly or alert drivers as they should
● Any other components that fail or malfunction and create a danger to vehicle occupants
Common non-safety-related recalls include the following:
● Radios, displays and other non-operating electrical issues
● Shocks, exhausts, batteries and other non-critical components that wear prematurely
● Body panels with rust or blemished finishes
● Air conditioning and heating systems that don’t work properly
● Emission components that don’t work correctly
● Any other components that fail or malfunction, but aren’t a safety issue
Vehicle manufacturers typically issue recall notices to a vehicle’s registered owner via letter. A recall notice will include a complete description of the issue and indicate the severity or seriousness of the recalled component(s). Recalls include information about the likelihood of injury, warnings, and what the manufacturer is doing to correct the issue.
When a recall is issued by the National Highway Traffic Safety Administration (NHTSA), recall repairs are typically performed at no cost because they are mandatory repairs. Most often, vehicle owners must take their car or truck to an authorized dealership or other service center approved by the manufacturer to have the recall issue corrected. The NHTSA provides a webpage to perform a vehicle recall check for owners where they can search vehicle recalls by VIN and other criteria.
What is a TSB?
A TSB is a notice that OEM vehicle manufacturers publish when components or systems malfunction, but don’t pose a safety concern. The bulletins are typically issued for problems that are discovered by repair technicians, but they can also be issued by OEM vehicle manufacturers. Because there may be multiple causes and a range of repair options, a vehicle issue can lead to more than one service notice.
TSBs are typically distributed to dealership service departments and body shops to help repair technicians correct an issue accurately and efficiently. Service bulletins are usually published specifically for a particular YMM and include a detailed explanation of the problem, symptoms and other related information. Because these documents are designed for use by repair technicians, having the most up-to-date bulletins will save time and expense for related collision repair.
What Are the Main Differences Between TSBs and Recalls?
Recalls are issued by the NHTSA or the manufacturer when an issue puts vehicle passengers and others at risk. Vehicle manufacturers are responsible for correcting recalled systems or components at no cost to vehicle owners, as mentioned earlier, regardless of the warranty status. Manufacturers must repair and/or replace faulty parts but can also be on the hook for a full refund in severe situations.
Technical Service Bulletins are issued by manufacturers for recurring, non-safety-related issues. The NHTSA documents these service bulletins, along with vehicle recalls by make and model, However, authorized dealerships aren’t required to correct issues free of charge because the issues aren’t safety-related.
Why TSBs and Recalls Are Important for Collision Repair
Because service bulletins and recalls provide in-depth OEM information for everything from diagnostics to replacement, performing a collision repair without the most up-to-date information could be costly.
For instance, if a technician did not have the latest OEM TSB and recall information and installs a $300 part instead of a five-minute wire trace and repair. the job will cost your shop more money and potentially result in an unsafe collision repair.
While many body shops won’t see much recall work, taking a proactive approach with TSBs can help create a healthier bottom line. That’s because most vehicle owners aren’t even aware of TSBs for their car or truck, so there’s a good chance they would appreciate your body shop letting them know about the issue. With the most current TSBs, your collision facility can perform safe, accurate repairs and provide a needed service for your customers.
Get On-Demand Access to the Latest Recalls and TSBs with SUN Collision Software
When your professional technicians access TSBs and recalls using SUN® Collision, our constantly updated OEM information takes the guesswork out of related collision repairs. With SUN Collision, it’s much easier to itemize repair procedures and standardize repair processes. SUN Collision provides updated TSBs and recalls on-demand to give your body shop a streamlined process for accurate, cost-effective repair and replacement.
Because TSBs and recalls include OEM information for troubleshooting, diagnostics and repairs, having the most up-to-date data is critical. Whether collision repair technicians use our stand-alone lookup tool or our intuitive search engine, Search Plus1, SUN makes it easy to pull up TSBs and vehicle recalls by manufacturer, VIN, and YMM. A comprehensive database of current TSBs and recalls ensures greater productivity and accurate, safe repairs, but you’ll also find extensive support for all kinds of repairs.
Here are a few of the features you’ll find with collision repair technology that provides answers for every type of repair, from recall and TSB issues to ADAS recalibration:
Common Collision Repairs
Vehicle recalls and TSBs can affect a range of systems and components, many of which are interconnected. That’s why even the most common collision repair should start with a vehicle lookup. Collision repair technicians can easily access the most current OEM information using familiar search terms such as YMM, symptoms, codes, components, and mileage. The resulting information lets technicians approach every collision repair with the latest and most comprehensive knowledge available.
Real Fixes
There’s a reason many TSB issues are first discovered by repair technicians. While manufacturers know their vehicles inside and out, collision and mechanical repair technicians are uniquely qualified to identify post-production issues. That’s why SUN Collision includes real fixes for both mechanical and collision repairs. With complete access to notes and records from over a billion past mechanical repairs and 45 million real fixes, real-world diagnostics and repair procedures are just a click away.
ADAS Diagnostics and Recalibration
Advanced Driver Assistance Systems (ADAS) continue to evolve year after year, and the technology behind ADAS can pose challenges in vehicle repair. The safety features in the latest vehicles rely on sophisticated computers, cameras and other sensors that are integrated with body panels, frames and other systems. That integration means ADAS repairs require a thorough understanding of the system as a whole and how to identify damaged or improperly calibrated components.
ADAS collision repair procedures require detailed, up-to-date OEM information for proper diagnostics, repair or replacement, and most of all, ADAS recalibration. 360-degree cameras and forward collision sensors are hi-tech components that rely on precise measurements and other data. That level of precision requires the latest, most detailed ADAS information available – and you can have it at your fingertips whenever you need it with SUN Collision.
Interactive Wiring Diagrams
From the advanced technology of ADAS to common collision procedures, the interconnected wiring in modern vehicles may be the single most important component encountered. When your body shop has access to the most detailed and up-to-date wiring schematics, diagnostics are more precise and repairs are more comprehensive.
Our interactive wiring diagrams are presented in an easy-to-read format that gives repair technicians big-picture overviews and the most minute details. With the latest wiring traces, component locations and testing processes, your body shop can have more skilled technicians and keep more work like ADAS repair in-house.
To learn more about how collision repair software can save time, reduce costs and streamline your workflow, we’d be glad to give you a quick but informative demo at your convenience. If you’d like more information, call SUN at 877-840-1973 and talk with a collision repair expert who understands the challenges of modern collision facilities.
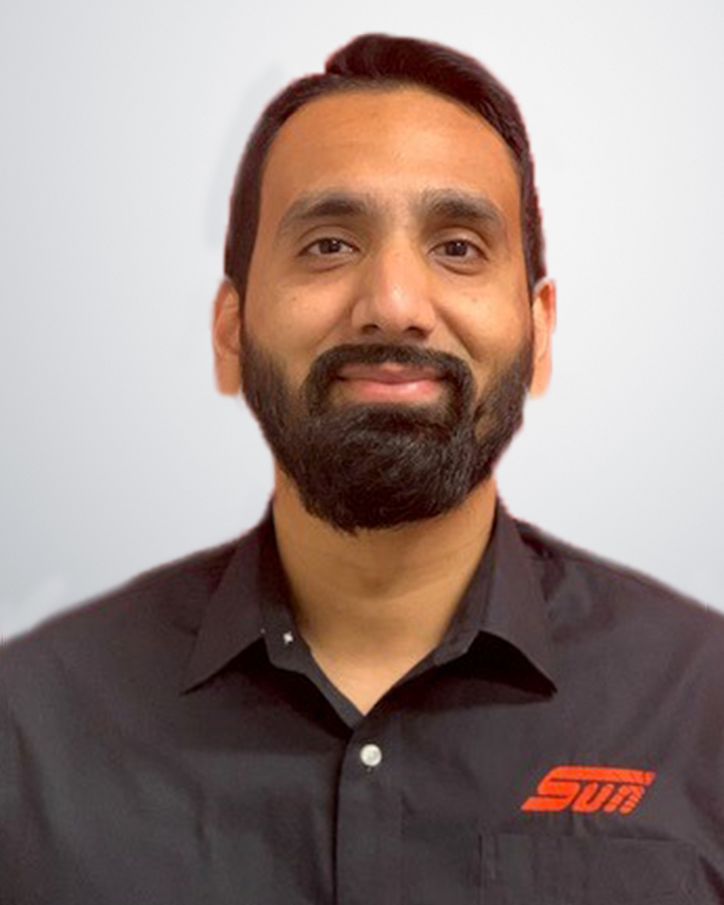
Kiran Wagh serves as Inside Sales Manager for SUN Collision and other Snap-on, Inc. brands, including Mitchell 1. He began his career at Snap-on in 2015 as an inside sales developer for Mitchell 1 and promoted to sales manager in 2019 for SUN Collision. Previously, he worked as a Demand Generation Specialist at Harte Hanks, where he led B2B lead generation campaigns with prominent networking and IT infrastructure companies. Kiran earned his degree in Aircraft Maintenance Engineering Level 1 in 2007 from the Hindustan Aerospace and Engineering college in Maharashtra, India, and later went on to study Information Technology at the Cisco Networking Academy.