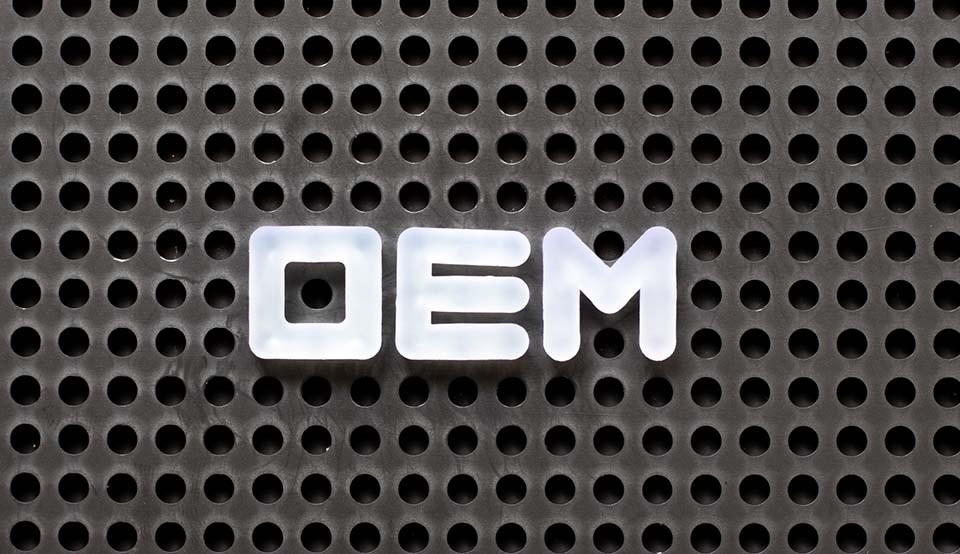
Do OEM Certifications Matter for Your Collision Repair Business?
By
|Does it matter if your collision repair shop isn’t OEM certified? After all, how many customers know what an OEM certification would mean for a body shop? If you’re about to retire or aren’t concerned about growing your business, then OEM certifications might not matter. But if you’re looking to increase your bottom line and stay competitive, certifications can help you save valuable time and money!
With advanced manufacturing, high-tech components and customers’ ever-increasing expectations, the face of collision repair is changing and evolving. In 2011, these changes spurred auto industry associations to create standardized OEM certifications for collision and other repairs. Industry leaders determined that OEM repair procedures should be consistently measured and monitored to ensure compliance with certification requirements.
If certifications seem like they’re solely aimed at driving sales of OEM parts, consider these two key reasons why certification is worth a look:
- First, most body shops need all the help they can get to work on advanced materials and systems. OEM certification opens a communication channel with auto manufacturers and typically includes perks like in-depth repair guidance and advanced notice of future innovations.
- Second, OEM certification can ensure more accurate and efficient collision repairs to reduce comebacks and increase customer satisfaction. A study by FCA a few years ago found that 60 percent of customers who received subpar collision repairs sold or traded the vehicle within a year — and even more switched auto brands!
There’s no doubt that cars and trucks are rapidly changing, and you can bet things won’t be any different next year and the year after. And just as automakers are using technology to innovate, today’s consumers are using technology to research businesses — and they’re getting savvier by the day. Informed customers care about things like certifications. The implication is clear whether customers understand the certification meaning: certified services are better than uncertified ones.
Dissatisfied customers have negative impacts on car manufacturers and body shops, so improving the customer experience should be a top priority for both. With OEM collision repair certification, not only could customers perceive your body shop to be the best, but the repairs they receive can also make that perception a reality!
The True Value of OEM Collision Repair Certification
So, is the ROI worth it? While it may be challenging to quantify the exact ROI of obtaining certifications, investing in equipment, training, and tools can provide invaluable knowledge and skills that can positively impact your business growth. OEM certifications can drive business, instill customer confidence, and create new revenue. But perhaps equally important, they can also promote safer, more accurate collision repairs and help protect your business. Meeting OEM requirements for repair procedures and documentation will always be a plus when your shop faces adversity.
Here’s a good way to get started — Check out a specific manufacturer’s certification requirements and make sure the certifications are available in your market. Note that some OEM certification programs that have been around for the last decade are already at maximum capacity.
Not only can you discover which certifications are available, but you can also compare the equipment, training investment, and other key elements. Once you have a handle on auto body shop certification requirements, you can make an informed decision about which ones are right for your body shop.
OEM Certifications in Your Body Shop
What is OEM certification? Simply put, a certified auto body shop is one staffed with collision repair technicians who are OEM trained to work on specific vehicles. OEM certification ensures that technicians are up-to-date with the latest technology and recommended repair procedures dictated by the auto manufacturers.
While investing in body shop technology, like SUN® Collision Repair Information, can return immediate benefits, the impact of OEM certification can take longer to materialize. Don’t assume your business revenue will magically increase because you’re certified. Since certified auto body shops are a relatively new thing [1], optimizing the certification status requires marketing and, above all, educating customers.
Many OEM certification programs include basic marketing support and a listing for your shop on a certification list. But to harness the full power of OEM certification, a certified auto body shop must help spread the word. While having your certification credentials and decals posted in your shop and on your website can drive business, it’s up to you to keep your unique selling point front and center.
A word of warning: if your interest in becoming certified is mostly for show, you may be better off skipping it altogether. Certifications hold value with consumers, but becoming a certified auto body shop can be a challenging endeavor that requires a significant financial and time commitment.mOEMs take the certification process seriously, and so should collision repair shops.
OEM Certifications Continue to Evolve
While some manufacturers’ certification programs are only recently getting off the ground, some are already unveiling new generations of their programs.These programs are constantly evolving with vehicle technology to create a safer experience for drivers, and provide insights for technicians of the latest developments and trends in OEM collision repair certification.
According to Body Shop Business, the latest focus on certification requirements regards documentation. Not a surprise to experienced body shop owners but an important topic to understand. The push for detailed collision repair documentation comes down to answering a simple question: Can you prove you performed a repair according to OEM repair procedures?
If you are serious about being a certified auto body shop, the answer to that question should always be “yes.” When that’s the case, providing the necessary documentation will be an easy requirement to meet. Acquiring certification as a body shop and incorporating advanced collision repair information can create an unbeatable combination, giving your shop a competitive edge.
Certified Auto Body Shops Will Have the Advantage
Technology moves fast, and if your body shop isn’t prepared to keep up, there’s no way it can continue to compete. Consider that about 70 percent of light-duty cars and trucks will have components and systems with internet connectivity. Combined with the pressure to make vehicles lighter, safer, and more economical, this advanced technology poses some serious challenges for collision repair.
A shift is taking place in the collision repair world in response to sophisticated materials like aluminum and carbon fiber and advanced systems like ADAS. Materials will continue to evolve and require new skills and knowledge. And because of the increasing power of internet connectivity, a scenario where customers can be automatically directed to the nearest certified auto body shop after an accident is a possibility.
No matter what the future holds for the auto industry, body shops with collision repair certification supported by the latest software will have the advantage.
OEM Certifications and SUN Collision
OEM collision repair information and OEM certification go hand in hand, and nobody delivers the most up-to-date information like SUN. The innovations that drive OEM certifications also drive us to create the most advanced collision repair technology available. From up-to-date diagnostics to interactive wiring diagrams, we provide resources for nearly every repair:
Common Collision Repairs
Make your typical repair procedures more manageable with the latest OEM repair knowledge. Repair technicians can quickly find the most current resources using familiar terms such as YMM, codes, symptoms, components, and mileage. The resulting information helps technicians complete common collision repairs more safely and accurately.
Real Fixes
Can you imagine what it would be like if your body shop had access to notes and records from over a billion past mechanical repairs? How about 45 million real fixes? When you invest in collision repair software, you get both. With access to Sun Collision Repair Information, real-world insights and guidance from industry peers who’ve been there and done that, are just a click away!
ADAS Repairs
ADAS continue to evolve not only in their complexity but also in their degree of interconnectivity. Modern safety technology increasingly relies on integrating safety features with frames, body panels, windshields, and other systems. The advancing technology can be a challenge, but when your body shop is well-versed in ADAS repairs and recalibration, repairs are much more manageable and efficient.
Materials Data
Manufacturers continue in their quest for lightweight and durable materials for building their latest models, and therefore are introducing components that didn’t even exist a decade ago. The ongoing innovation is good news for drivers, but maybe not for your body shop mechanics — unless you’ve invested in OEM certifications and repair technology. When you have real-time information, you can work with even the most advanced materials confidently.
Implementing OEM certification is one of the best ways to ensure your body shop is performing the safest and most accurate repairs possible. The best way to do that and meet the latest vehicle technology head-on is to put advanced collision repair technology to work in your body shop.
Let SUN Collision show you how to stay a step ahead of the vehicle technology curve for better collision repair today and tomorrow. Get your free no-obligation demo or talk with a collision repair expert at 877-840-1973 to see how having on-demand OEM information can transform your body shop.
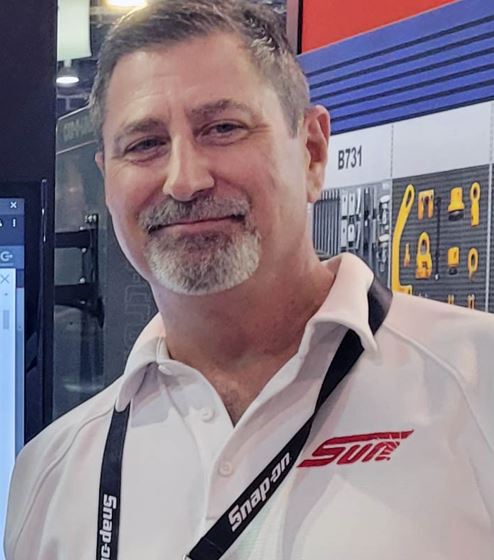
Ross Whiteley, Product Manager for SUN Collision, has held roles of increasing responsibility at Snap-on over the past 13 years. He joined SUN Collision’s sister company, Mitchell 1, as a Product Contact Support Representative in 2010 and was later promoted to Client Services Manager. He began his career after high school as a UPS driver in 1997 and went on to earn a Bachelor’s degree in Business Management and an MBA in BA in Project Management at Purdue University in 2015. In the interim, he held various positions in the auto industry, including roles as Service Consultant at Lithia Chrysler Dodge and Assistant Service Manager at Cascade Auto Center.