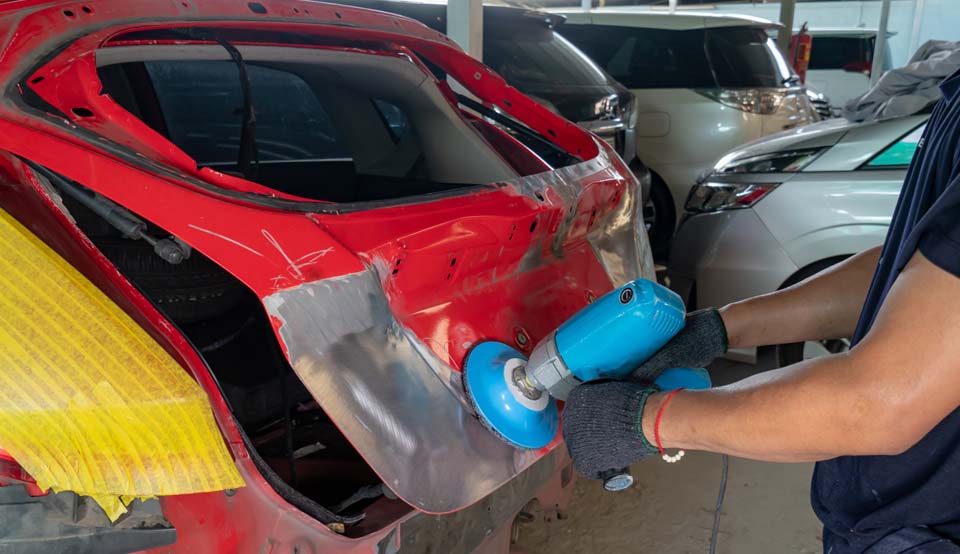
Best Practices for Fast-Tracking Auto Collision Repairs
By
|Performing and tracking repairs efficiently requires more than collision repair expertise and a space to work. Even the most experienced collision repair technician can only perform repairs as fast as the shop’s limitations allow. To fast-track repairs, the first step is to minimize the limitations in your shop that slow down the repair process.
So, what circumstances in your shop could be slowing down the repair process?
The availability of parts is a common challenge, especially since the pandemic. High demand, back orders, and even the weather can delay getting the parts you need to perform repairs. While there’s not much you can do about the limited supply of components, you can put technology to work in your shop to better manage the problem and fast-track maintenance needed.
Other challenges that prevent many body shops from performing and tracking repairs efficiently include scheduling, collision technician proficiency, and shop-specific challenges. There are several ways to improve scheduling and technicians’ skill sets to fast-track repair in your shop.
SUN® Collision Repair Information provides the latest repair software to improve your workflow management, technicians’ accuracy, and collision repairs’ efficiency. But there are shop-specific hurdles that have little to do with technology or knowledge, and addressing them can ease the maintenance of tracking repairs.
Fast-Tracking Repairs Requires a Solid Foundation
Nothing can replace the years of experience performing collision repairs in your shop, but even the most seasoned collision technician can be more efficient. Not only can improving collision technician efficiency enhance the productivity of your body shop, but evaluating and refining your shop’s processes can also contribute to a more streamlined repair tracking system. Unfortunately, when cycle times are high, and everyone is working as hard as possible, the problem often lies in wasted time and outdated collision repair procedures.
Even when professional technicians have the advantage of being able to start a repair promptly and work uninterrupted, without a well-designed strategy, they can lose their focus. Technicians are only human, so they will create unnecessary interruptions and deviate from the recommended repair process without realizing it.
To provide an accurate, quick car repair and get your customers smiling out the door.
A typical example of this behavior is a repair technician who works on two or three repairs simultaneously in a misguided attempt at greater efficiency. The results range from over-production of repair materials to inaccurate repairs—and productivity can actually decrease. It’s challenging enough to track a repair, much less two or three simultaneously!
When your shop’s repair processes are consistent and efficient, greater productivity is a natural byproduct. Don’t leave productivity solutions up to your technicians. They are professionals whose job is to perform safe and accurate collision repairs. It’s your job to give them the tools and the knowledge necessary to work efficiently and productively; to provide an accurate, quick car repair and get your customers smiling out the door.
Where do you start? Looking at how your body shop is laid out and how vehicles move through the repair process is your first stop. When your operations and collision repair shop aren’t efficient, the result is less productive and often unhappy collision repair technicians. But how can you figure out where the inefficiencies and bad processes come into play in your body shop?
Ask Your Technicians!
Get Started on the Right Foot
Managing, administrating, and other responsibilities can be quite time-consuming, so it’s unlikely you’ll be as hands-on as your employees. The technicians who tackle collision repairs every day can provide valuable insights into where the problems lie. Ask your technicians about what processes slow things down Here are a few questions you could throw their way:
- Is it never knowing when parts will arrive?
- Are there problems with how the body shop is laid out?
- Is collision repair information outdated or hard to find?
Start Today — There are collision repair best practices you can implement to make your body shop more efficient right away. But if you want to make those changes last and optimize your collision repair center and repair processes, ask your technicians. This type of communication should be a staple of how you run your body shop. The feedback you get and the changes you make can fast-track repairs and make your facility a better place to work.
Maintain a Proper Workflow with Accurate Scheduling
Now that you have a handle on the challenges your technicians are facing, you can begin making changes to fast-track repair jobs. Your body shop won’t transform into a streamlined collision repair facility without careful planning and hard work, but there is something you can do right now that can make a difference.
Scheduling may be the critical element for productivity and your body shop’s success. Faulty scheduling can result in overwhelmed repair technicians, disgruntled customers, and slow-track repair processes. Too much work can be as bad as too little, so balancing the workload is vital. The only way to keep a balance is to schedule repair jobs based on your shop’s capacity.
It’s essential to understand your body shop’s capacity for accurate projections and scheduling. To get you started, here are some key considerations when creating your schedule:
- Can your facility handle four repairs each day or ten?
- Are you fully staffed, or is one of the repair technicians on vacation?
- If you’re short-staffed, have you made adjustments and communicated them to the paint and other departments?
You can’t predict the workflow with any certainty, but you can schedule repair jobs to maintain a balanced workload and timely repairs.
Invest in Your Collision Repair Technicians
Communicating more effectively with your technicians, welcoming feedback, and getting your shop and processes up to speed will work wonders. Once your body shop is on the fast track, the best way to maintain your strong position is to invest in your repair technicians regularly. How? By providing the latest OEM information and other resources to sharpen their skills and stay current.
Year after year, vehicles and the processes to repair damage become more advanced. These innovations require new knowledge and skills that can only be found with the latest OEM information. The line between collision and mechanical repairs has all but disappeared because even a seemingly minor accident can result in collateral damage to a range of systems and components.
Invest in SUN Collision and give your technicians the modern tools and information they need to work on increasingly complex repairs. From more accurate repairs to more motivated technicians, collision repair technology could be one of the most important tools in your body shop.
SUN Collision is Your Fast-Track Toolbox
SUN Collision repair software is an all-in-one toolbox full of fast-track repair resources that are constantly updated. With up-to-date OEM information only a click away, your collision repair procedures will be as advanced as the vehicles you repair. When you put advanced collision repair technology to work in your body shop, you can perform safe, accurate collision repairs and enjoy the associated benefits:
- Reduced comebacks
- Decreased cycle times
- Higher quality repairs
- More knowledgeable and skilled technicians
We make advanced collision repair software features like OEM service manuals, common repair procedures, and other up-to-date information easy to find and understand. How easy? If you know how to use Google, you know how to use our proprietary search engine, 1Search Plus™. Our intuitive collision software speaks your technicians’ language so they can fast-track repairs from diagnosis to completed projects.
Take a closer look under the hood and explore our key features included in your SUN Collision Repair Information:
Body and Frame
Critical information on the latest sectioning procedures, structural repairs, and other information is right at your fingertips. Because our repair software is automatically updated, you always have the knowledge and tools you need to perform even the most advanced collision repair procedures.
Materials
Modern vehicles mean modern, advanced materials that may not have existed only a few years ago. SUN Collision provides the OEM information you need to work with adhesives, high-strength steels, plastics, aluminum, composites, and more. Comprehensive, up-to-date data for materials, paint, and finishes are just a click away.
ADAS
ADAS collision repairs don’t have to be a mystery when you have accurate and current information. The most up-to-date ADAS information will help your body shop keep up with safety features year after year. You’ll find all the resources you need to perform accurate ADAS repairs from diagnosis to recalibration.
OEM Service Manuals
If your body shop’s service manuals are all over the place collecting dust and grease, we have a pleasant surprise. The next time you’re training a new technician or verifying a repair procedure, just click a button and access OEM service manuals on-demand.
Interactive Wiring Resources
When your body shop is working on recent model vehicles, interactive wiring diagrams are a must. Immediate access to up-to-date, detailed digital wiring diagrams that include related components and testing processes, lets you fast-track repairs easily.
Real-World Mechanical Repair
Light mechanical work can be a lucrative and simplified process when your technicians have the real-world repair information found in collision software. We can help your body shop keep more repairs in-house with in-depth diagnostic and procedure information for various mechanical repairs.
Get on the Fast Track with Collision Repair Technology
If you’re ready to fast-track collision repair, SUN Collision ensures you get the return on your investment you expect. Get your free demo of the industry’s most advanced collision repair technology today. We’re ready to prove our innovative collision repair software in your body shop with answers for every type of repair. Want to find out more? Call 877-840-1973 or visit us here to start fast-tracking repairs today!
Let SUN Collision show you how to stay a step ahead of the vehicle technology curve for better collision repair today and tomorrow. Get your free no-obligation demo or talk with a collision repair expert at 877-840-1973 to see how having on-demand OEM information can transform your body shop.
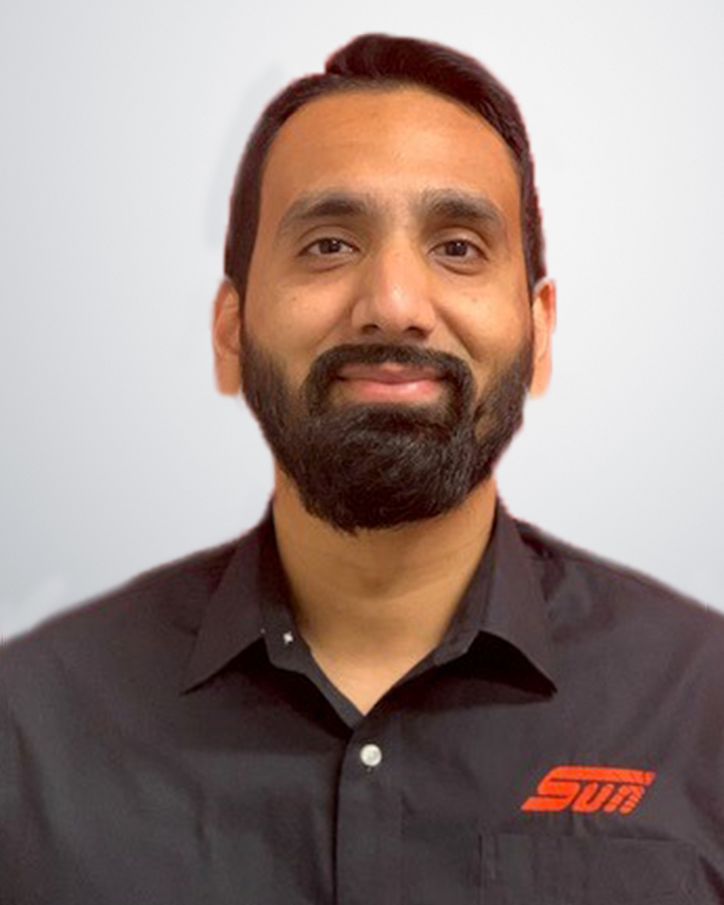
Kiran Wagh serves as Inside Sales Manager for SUN Collision and other Snap-on, Inc. brands, including Mitchell 1. He began his career at Snap-on in 2015 as an inside sales developer for Mitchell 1 and promoted to sales manager in 2019 for SUN Collision. Previously, he worked as a Demand Generation Specialist at Harte Hanks, where he led B2B lead generation campaigns with prominent networking and IT infrastructure companies. Kiran earned his degree in Aircraft Maintenance Engineering Level 1 in 2007 from the Hindustan Aerospace and Engineering college in Maharashtra, India, and later went on to study Information Technology at the Cisco Networking Academy.
Recent Blogs
- Technician Retention: The Key to Growing Your Collision Repair Business
- SUN Collision Integrates with Manager SE / ShopKey Shop Management Systems
- SUN Collision Announces Return of its ‘Thank You Thursdays!’ Sweepstakes
- SUN Collision to Showcase Auto Body Repair Innovations at SEMA
- SUN Collision Congratulates Anthony McNee, Winner of the Inaugural Best Repair Planner/Estimator Award